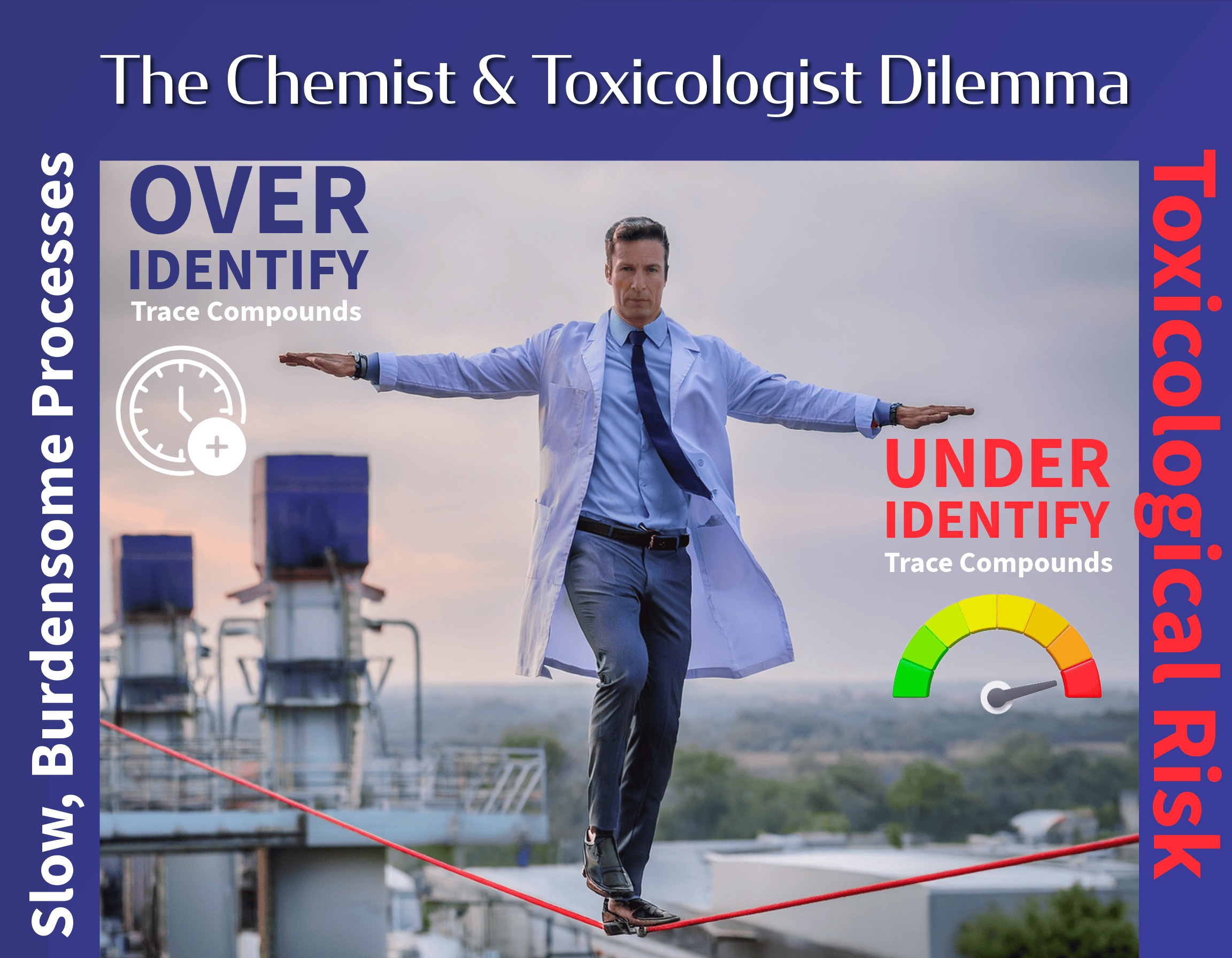
Balancing Analytical Uncertainty and Toxicological Risk Assessment
Tentative Identifications in Medical Device Chemical Characterization Analytical chemical characterization and toxicological risk assessment are essential for evaluating the risk posed by chemicals that may be present in medical devices. As detailed by ISO10993-17 and ISO 10993-18, this process can support the biological safety of a device through assessment of the toxicological risk of extractables […]
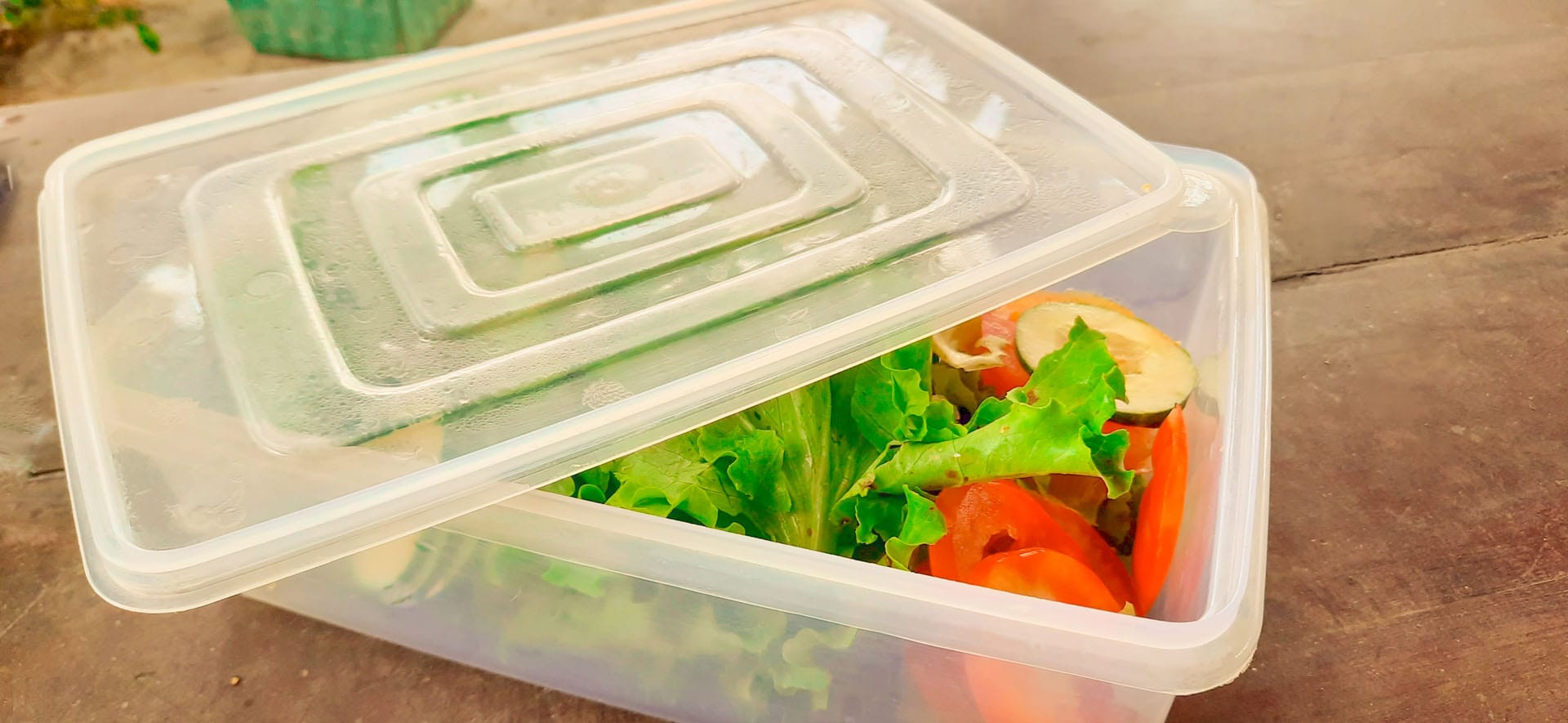
Potential Changes to the Generally Recognized as Safe (GRAS) Program
Background: The GRAS Framework The Food Additives Amendment to the Federal Food, Drug, and Cosmetic Act (FD&C Act) was established by Congress in 1958. In the Code of Federal Regulations, the rules that the FDA applies to food additives are spelled out in sections 21 CFR 170.3 and 170.30. A food additive is considered to […]
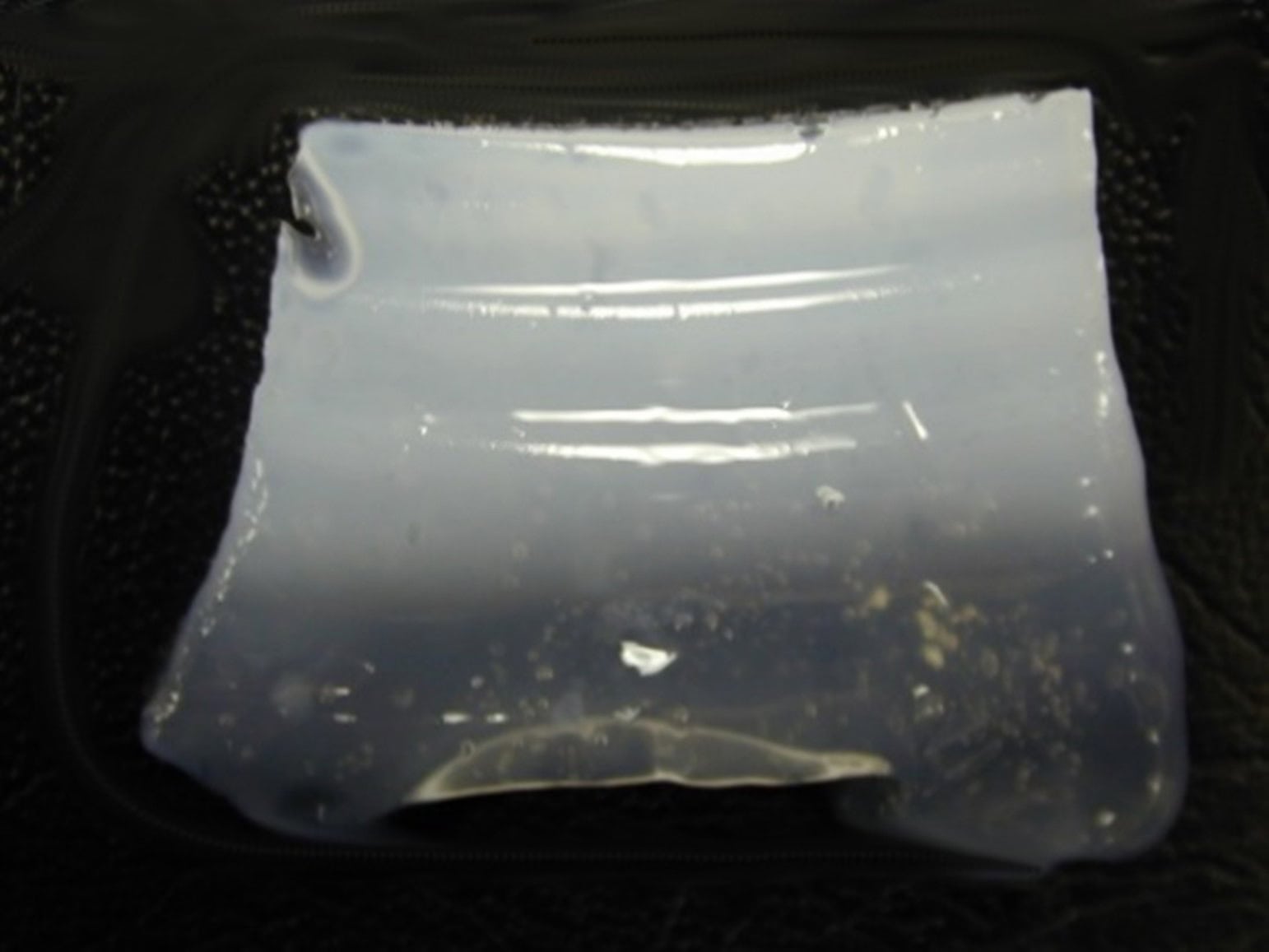
ASTM Workshop on the Characterization of Hydrogel Medical Devices: Key Takeaways
On May 6, 2025, the ASTM Workshop on the Characterization of Hydrogel Medical Devices brought together researchers and engineers to discuss current test methods for hydrogels in medical devices. Led by Stephen Spiegelberg of Cambridge Polymer Group, the workshop focused on current test methods, industry challenges, and the need for new standards. Why Are ASTM […]
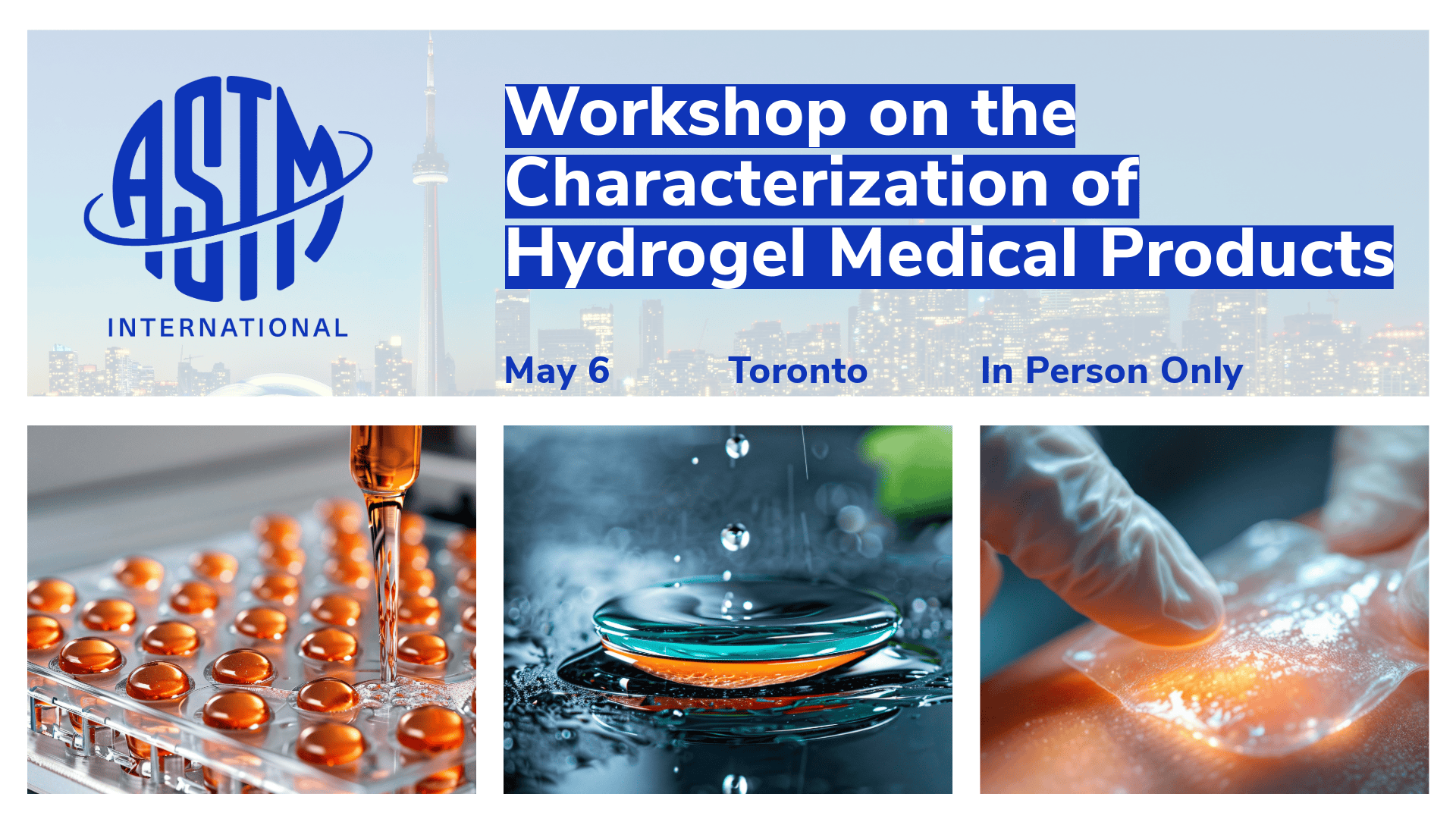
ASTM Workshop on Hydrogel Characterization
ASTM International will host the Workshop on the Characterization of Hydrogel Medical Products on May 6, 2025, in Toronto, Canada, during the spring meeting of the ASTM Committee F04 on Medical and Surgical Materials and Devices. This event brings together leading experts to discuss best practices, emerging analytical techniques, and the urgent need for standardized testing methods […]
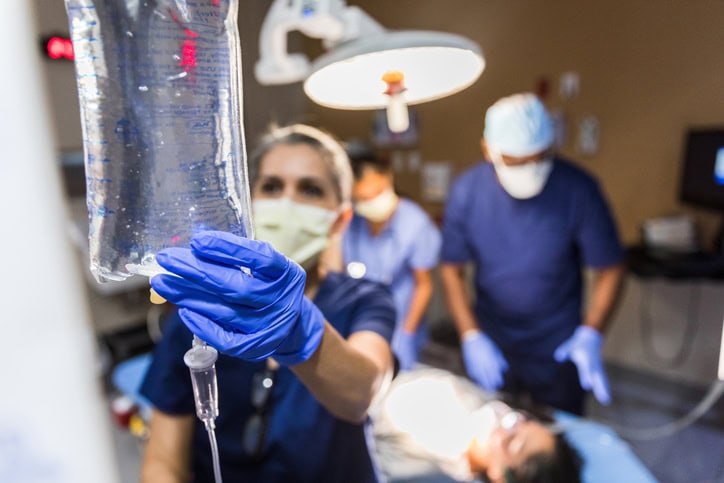
Microplastics in Infusion Bags
Microplastics have become a pressing topic in environmental and health discussions, with increasing attention from the media and scientific community. These tiny plastic particles, typically defined as ranging in size from 1 micrometer to 5 millimeters, can be composed of various types of polymers and are now being detected in an array of consumer products. A recent […]
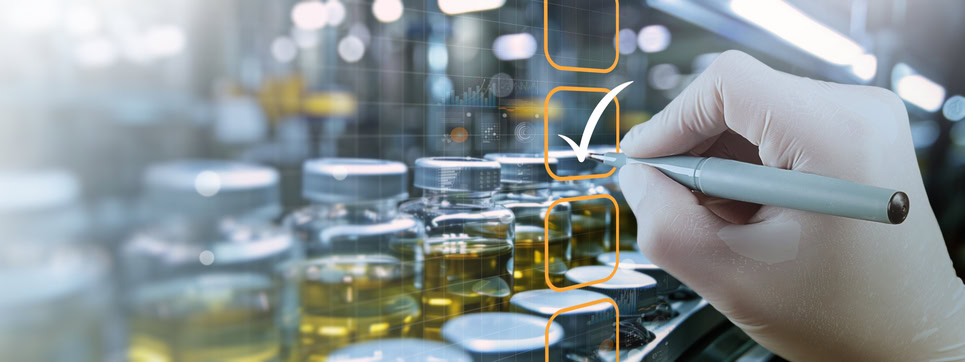
Ensuring Trustworthy Third-Party Lab Data for Regulatory Success
Companies regularly rely on third-party laboratory testing data to support regulatory medical device and pharmaceutical submissions, particularly when lacking in-house expertise or facilities. The credibility of these third party laboratories is crucial to regulatory success, but recent actions by the FDA highlight the risks associated with unvetted or noncompliant third party data. Escalating FDA Scrutiny […]
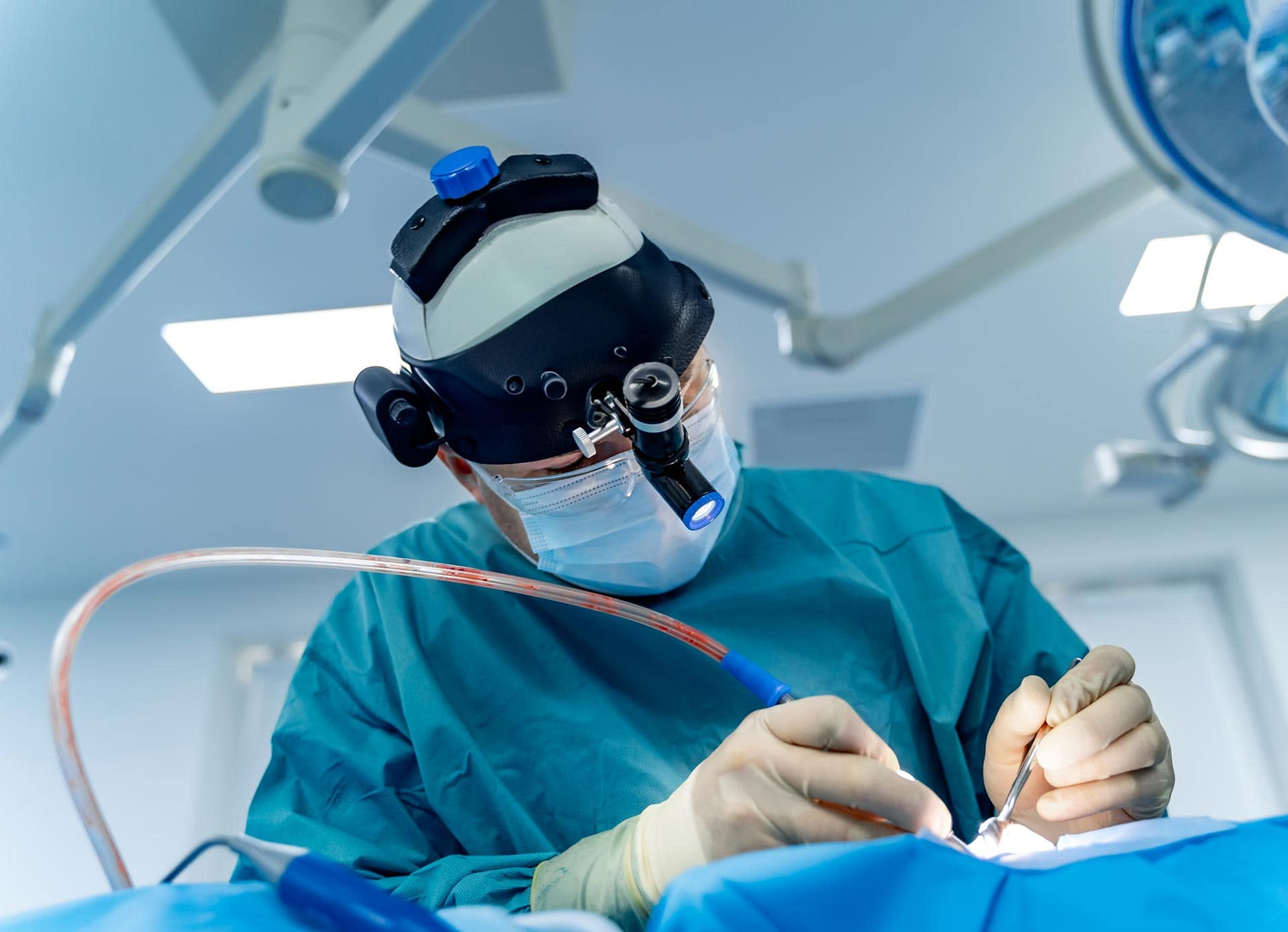
Thoughtful Design in Surgical Lighting: Balancing Usability, Durability, and Sustainability
Traditional headlamps (worn above) are cumbersome and don’t accommodate face shields. A groundbreaking surgical task light has been introduced by MezLight in collaboration with Syensqo[1], demonstrating a thoughtful approach to product design by considering key factors such as: Customer needs Sustainability concerns Environmental durability Material suitability Addressing Customer Needs: Enhanced Usability and Safety Traditional surgical […]
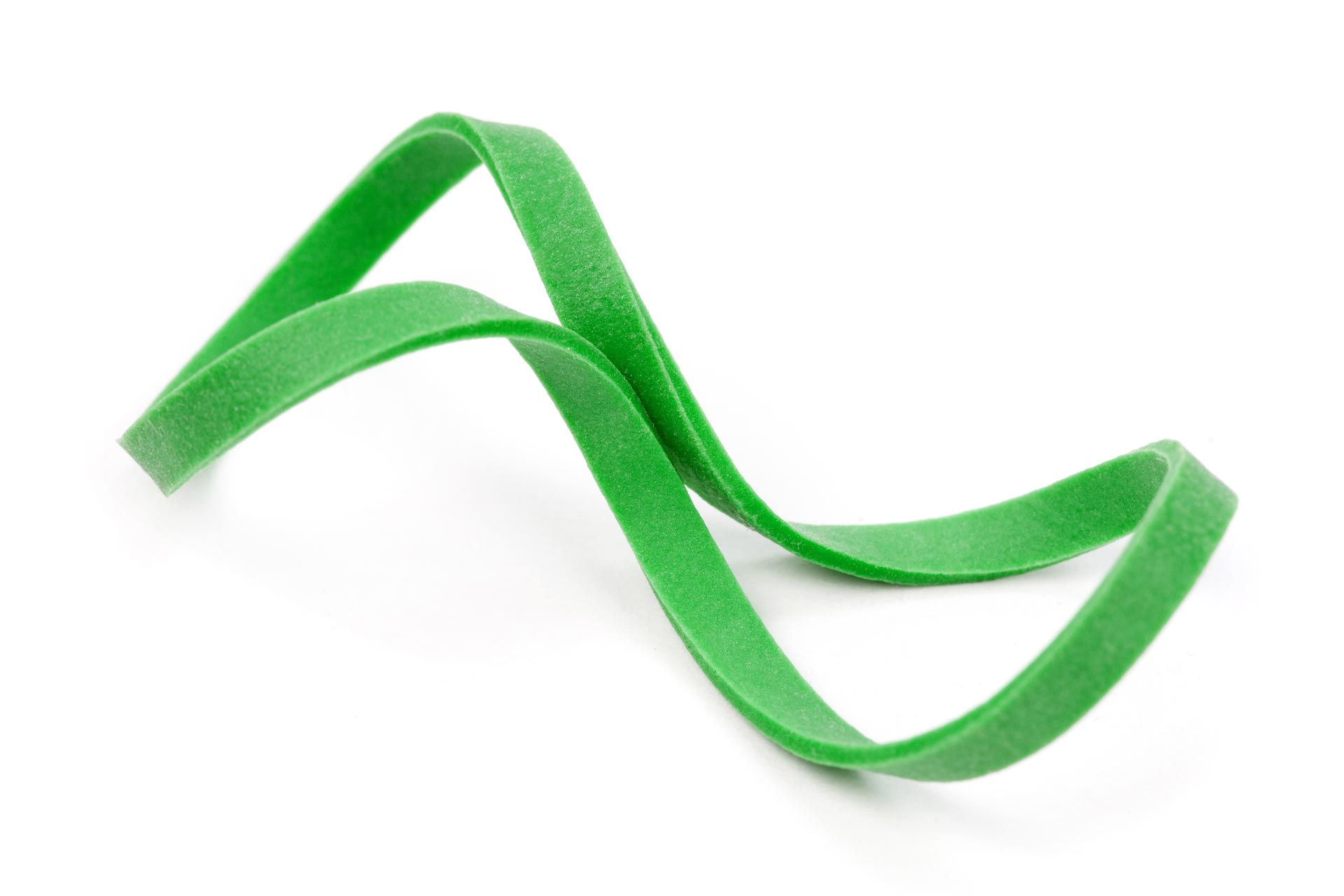
Celebrating Rubber Band Day
Every year on March 17th, we commemorate the invention of the rubber band, patented by Stephen Perry in 1845. This innovation followed Charles Goodyear’s groundbreaking discovery in 1838 that adding sulfur to polyisoprene creates crosslinks, significantly enhancing its elastic properties. This breakthrough led to the development of rubber tires. Composition of Rubber Bands Rubber bands […]
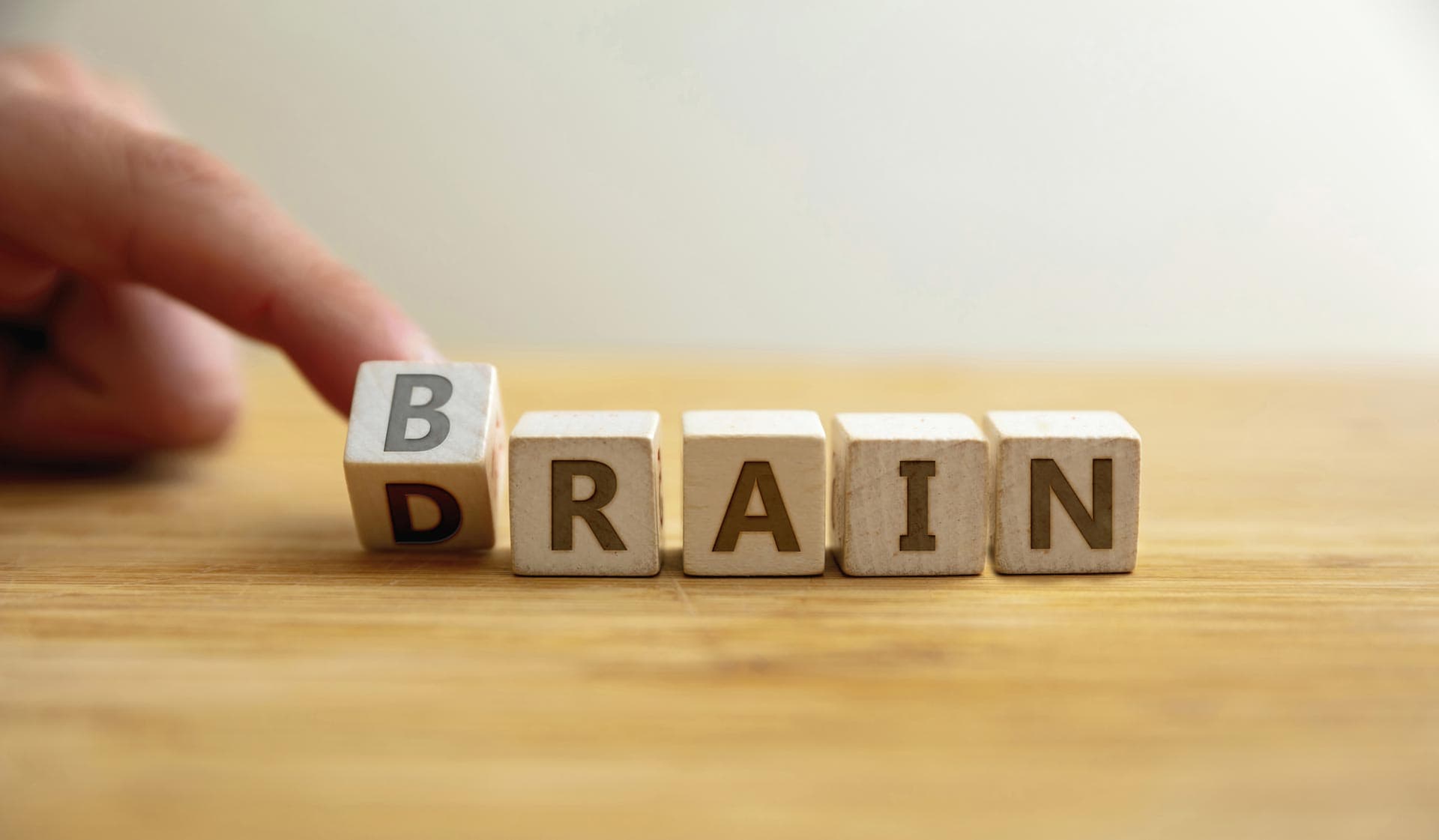
FDA Layoffs: Impact on Medical Device Review and Patient Safety
Over the February 15-16, 2025 weekend, the new U.S. administration laid off a substantial number of FDA reviewers from the Center for Device and Radiological Health (CDRH), the branch that reviews the safety and efficacy of new medical devices, including hip and knee implants, cardiovascular and respiratory devices, ophthalmological treatments, wound care, and thousands of […]
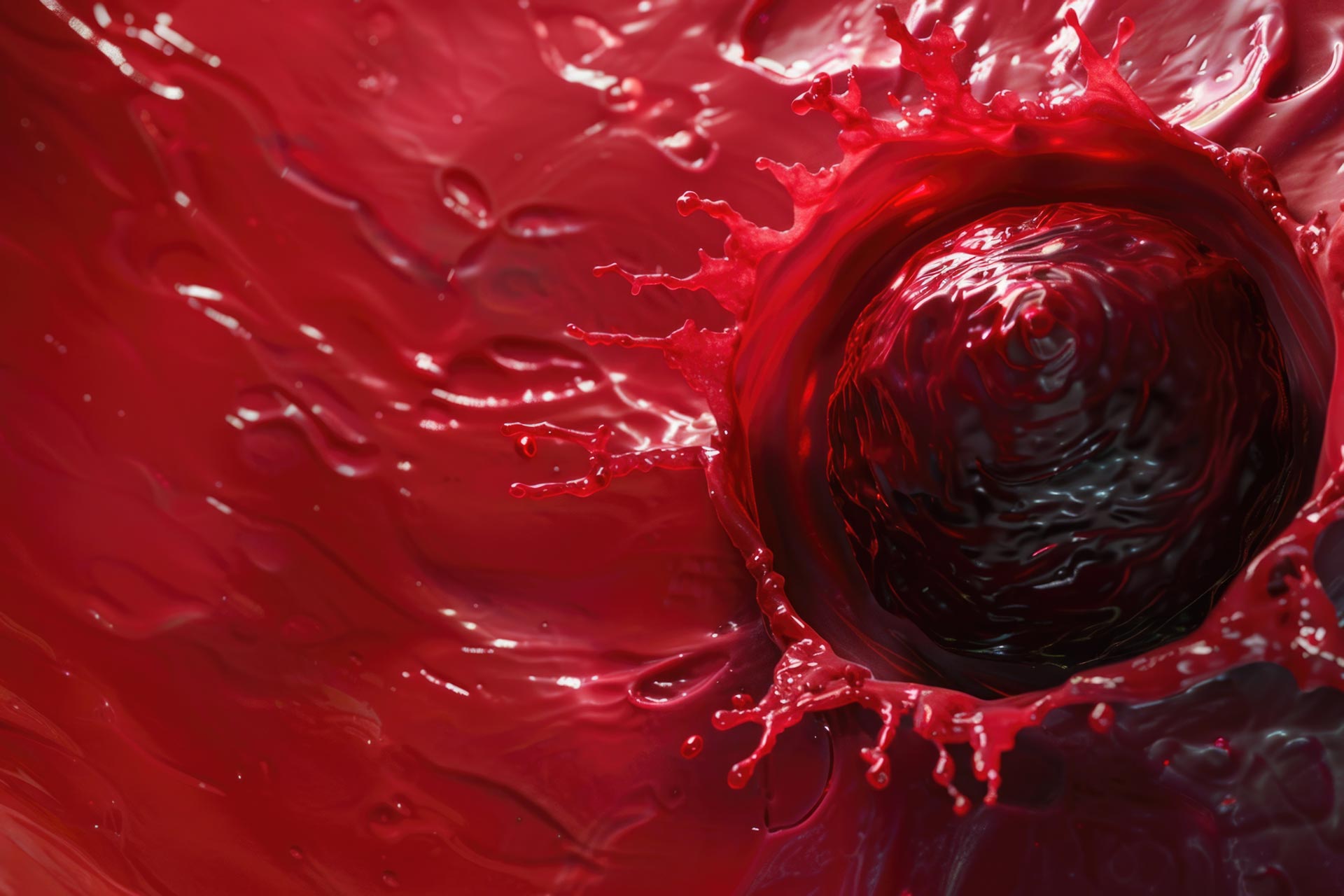
Quantifying Rapid Rheological Changes
Blood vessel with hemostatic agent In the world of material science and product design, understanding and measuring rapid rheological transitions is crucial. These transitions, which can be triggered by various stimuli such as UV light, electrical fields, or chemical interactions, play a significant role in applications ranging from hemostatic agents to 3D printing materials. While […]